在航天器制造领域,"失之毫厘,谬以千里"的严苛要求使得零件加工精度成为决定任务成败的关键因素。随着太空探索向更深、更远领域拓展,传统加工技术已难以满足高密度、高性能零件的制造需求。
超声波二维振动平台的引入,正为航天零件加工带来革命性突破。
一、突破传统加工极限
超声波二维振动平台通过高频振动(通常15-40kHz)在切削方向叠加微小的振动量,使刀具与工件之间形成周期性微切削。在航天铝合金零件加工中,该技术可使表面粗糙度从Ra0.8μm降至Ra0.1μm以下,刀具寿命延长3倍以上。在钛合金加工领域,振动引起的自锐效应有效避免积屑瘤形成,使加工效率提升40%。
振动平台的创新之处在于其可编程特性。控制系统可通过CAD/CAM软件实时调整振动频率和幅度,针对不同曲面特征实施动态优化。这种智能调控能力使复杂结构的深腔、薄壁零件加工成为可能,满足航天器轻量化设计需求。
二、助力高精度加工创新
在微型航天零件加工场景中,振动平台展现特殊优势。某卫星用微型齿轮加工案例显示,采用二维振动平台后,齿面波纹度从2μm降至0.5μm以内,关键尺寸精度稳定在±5μm以内。在高精度镜面加工中,振动辅助工艺使面形精度达到λ/10量级,满足空间光学元件的要求。
振动技术对加工材料的热敏感性问题提供了解决方案。在高温合金零件加工时,振动能量促进了切屑快速脱离,有效降低切削温度30%-50%,避免了热影响区的形成。这一特性对碳纤维复合材料加工同样适用,显著提高了层间结合强度,降低了分层风险。
三、智能制造系统集成
现代超声波振动平台与物联网技术深度融合,实现加工状态实时监控与自适应调整。通过传感器网络,系统可监测振动参数、切削力、温度等20余个指标,当检测到异常时立即优化参数设置。大数据分析功能可根据历史数据预测刀具磨损趋势,提前预警维护需求。
四、超声波二维振动平台实拍图展示
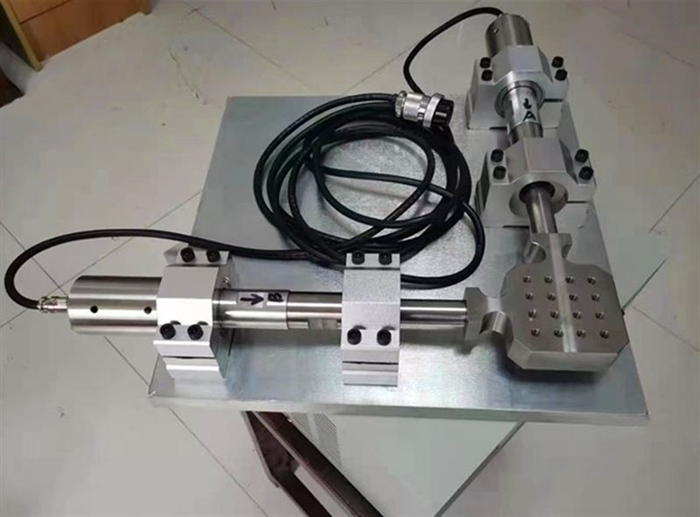
未来,随着振动频率提升至兆赫兹级、功率密度增加,其在航天零件微细加工领域的应用将更加广泛。这种智能加工技术的突破,不仅提升了制造精度与效率,更为我国航天装备的高质量发展提供了坚实的技术支撑。